DMAIC - Define, Measure, Analyse, Improve, Control
DMAIC - Define, Measure, Analyse, Improve, Control
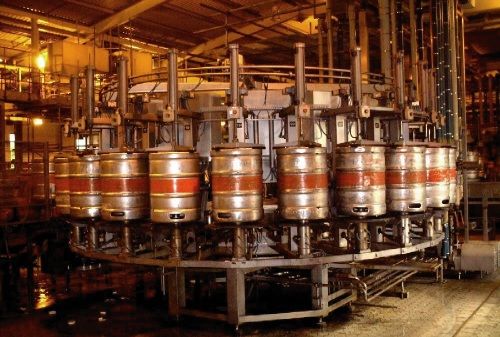
DMAIC refers to a data-driven improvement cycle used for improving, optimizing and stabilizing business processes and designs. The DMAIC improvement cycle is the core tool used to drive Six Sigma projects. The overall process contains a suite of tools that can be used to drive process improvement. The DMAIC cycle can be used both for large programmes and for smaller improvement tasks. The Managing Director of Zero Carbon Engineering has been involved in continuous improvement from 1996 – and has been both a coach and participant working internationally for the twenty years with several large companies. This description of DMAIC is laid out as by the American Society of Quality. (ref: The Certified Six Sigma Black Belt Handbook ISBN 8174890521)
DEFINE: Define starts the cycle with tools that look at the requirements both of customers and the business itself to define what are the key issues the improvement process is trying to address. It looks to set up reliable and valid data collection methods, and uses mapping process such as SIPOC, Process Maps, Value Stream Maps, Critical to X, Cause and Effect Matrices, Process Efficiency and Work in Progress, Takt Time and Waste (Hidden Factories),
MEASURE: Looks at measurement systems, calibration and error, measuring process and enterprise performance, using statistical methods, distribution of results and statistical testing, process performance and capability as tools to carry out reliable and valid methods of capturing data at the beginning and end of the improvement cycle. The key is to have a firm measurement of where the project started so improvement can be measured.
ANALYSE: Looks at analysing data collected at various stages of a project. This uses statistical tools to correlate results, carry out regression analysis, test for variances, proportions and goodness of fit of data. It also uses tools such a Failure Mode and Effect Analysis (used as part of a reliability centred maintenance process), root cause analysis, and waste analysis (MUDA).
IMPROVE: Looks at improving a process using the data collected, measured and analysed to improve the problems from the define stage, The define stage starts by defining experiments that will set hypotheses as to what is causing a given issue – and thus if corrected, will bring about an improvement. The improvement methods include tools such as waste elimination, cycle time reduction, Kaizen / Kaizen Blitz (small team improvements) and theory of constraints,
CONTROL: Looks to maintain what has been achieved in the improvement cycle and prevent it from unravelling in the future. This involves tools such as process control charts to monitor a process, managing process inputs to guarantee the output, total productive maintenance – putting in place visual tools, work place organisation and introducing a zero loss concept and finally reviewing the improvement process itself to capture learnings for the future,
Control also includes "retained knowledge tools" such as Porters 5 Forces, Portfolio Architecting (for managing a business wide Six Sigma programme), Hoshin Planning, TRIZ (for innovation) and Pugh Analysis.