Low Loss Transformers and Voltage Optimisation
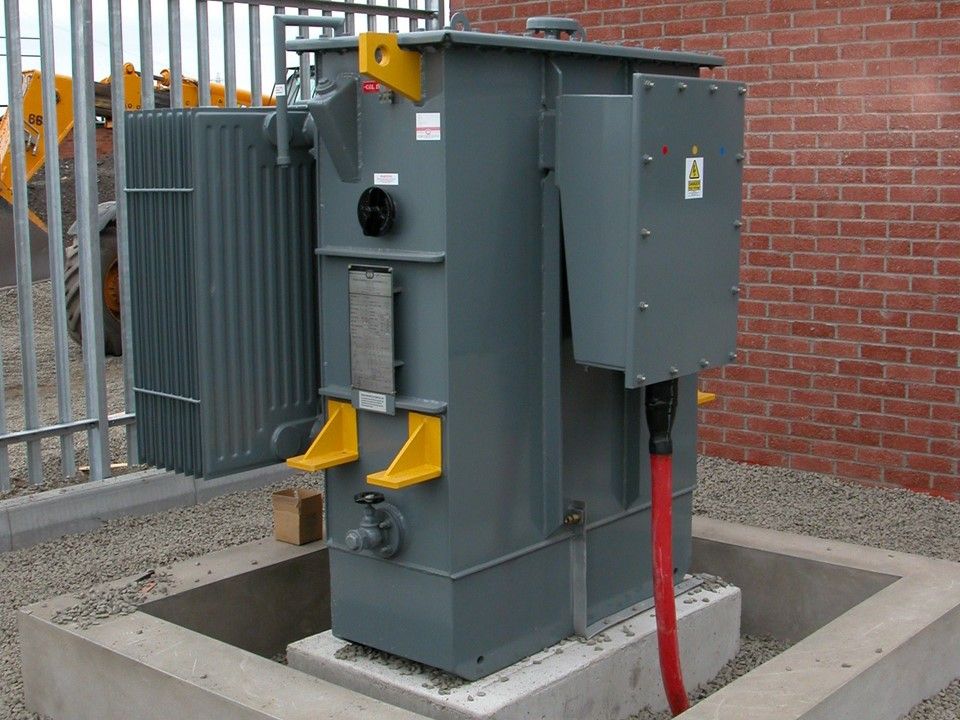
Zero Carbon Engineering has had considerable experience over the years in reducing the usage of electricity both in retail and in FMCG.
Electricity is moved around the UK initially in the transmission system at voltages of 400,000volts to 275,000volts and then down to local distribution networks (132,000volts and below). The commonest form of “low level” high voltage is 11,000volts.
There are a number of ways to reduce cost and carbon in the supply of electricity: -
- Firstly for an industrial site with a significant load (over 100kW) it is worth considering installing an High Voltage supply (11,000V) and installing your own 11,000volt to 400volt transformers. Purchasing electricity at high voltage is cheaper than purchasing at low voltage, as with low voltage you do pay for the network operators equipment or hysteresis losses.
- Over the last ten years, transformer technology has moved on with low and now super low loss transformers coming onto the market. These use materials such as amorphous metals to reduce the magnetic core flux in the transformer. A traditional oil filled 1000kVA transformer would absorb c12kW of power (and therefore heat) in hysteresis losses. A super low loss transformer comparably only absorbs c7kW – running 40% more efficiently and with less heating up of the transformer.
- Prior to the UK joining the European Union, the UK voltage delivered to ‘domestic equipment” was nominally 240V 50Hz +/-6% (254V to 225V).
Europe operated at 220V 50Hz with a variety of tolerances.
In 1995 an EU drive to harmonise voltages came about so that electrical equipment could be moved across borders without risk. In reality, the whole thing became a compromise with an agreement that the harmonised voltage would be 230V +/-10% (253V to 207V).
This provides an opportunity because on sites where either the district network operator is delivering 240V or the site has an old transformer delivering 240V, there is an opportunity to reduce the voltage and any equipment built and installed after 1995 will continue to operate.
For items such as non-LED lighting, electric motors (not on variable speed drives) and some process plant it is possible to achieve a up to a 9% power saving without impacting function.
This can either be done either by:
- On High Voltage supplies by purchasing a transformer with suitable tappings so that transformer can have its output stepped down to 400V (or below if feasible).
- On High Voltage supplies there are now transformers on the market that can electronically adjust their ratio to maintain a constant voltage output and take advantage of any changes in the high voltage supply voltage. This tends to rise up slightly at night at times of low load and drop slightly during the day at times of high demand.
- On Low Voltage (400V/240V) supplied sites install a small transformer – called a voltage optimiser – to reduce the supply on site.
Typically on a low voltage site switching to high voltage, a payback of c.2 years is achievable, and similar savings are achieved on voltage optimisation – bring the payback down to 1 year.