Control - Small Group Activity - 5S / Control Charts / TPM
The Managing Director of Zero Carbon Engineering was coached in 5S, Visial Factory, setting up SOP and maintenance systems and training in 1996.
Since then he has carried out multiple implementations in FMCG operations.
This process locks the benefits of any preceeding DMAIC steps in place by providing a structure that retains knowledge and organisation.
After the improvement activity is complete, the control phase includes things such as finalising work instructions and standard operating procedures, producing control charts to manage critical process inputs and outputs, creating visual aid boards such as the one to the right - which shows useful live information to the team using it - and gives them ownership by maintaining it. The whole process is then backed up by training, including a measure of how well compliance to the new process is maintained.
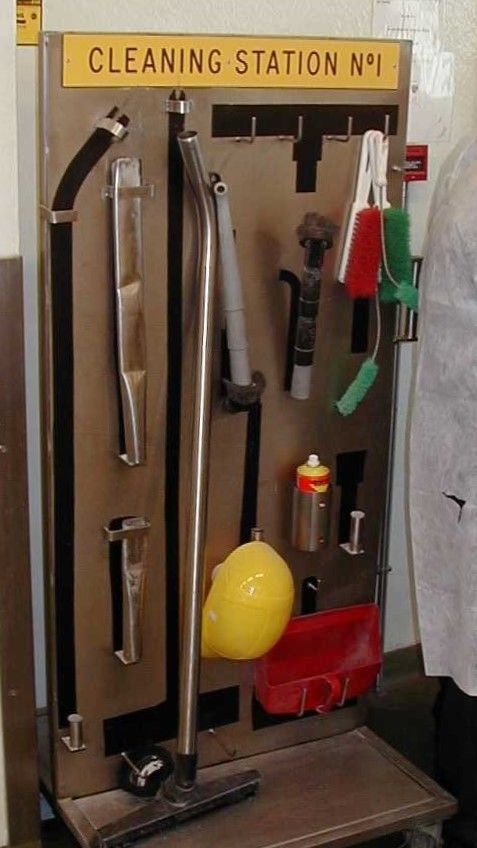
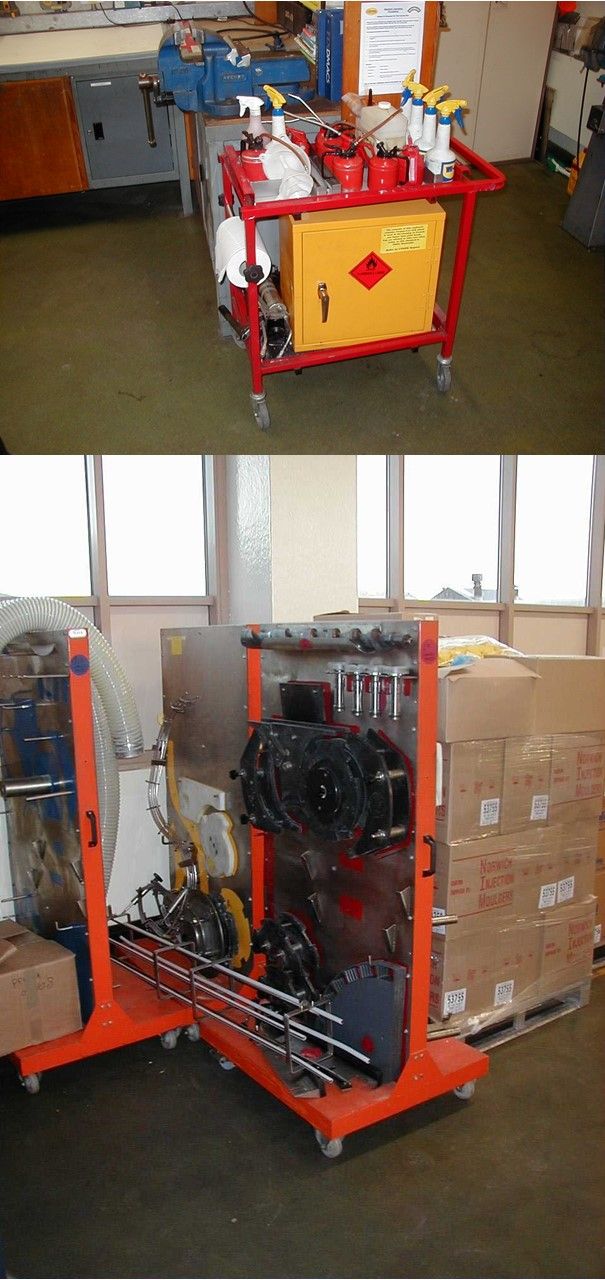
As part of the control process, the work place is also standardised with activities such as 5S (Sort, Set in Order, Shine, Standardize, and Sustain) which gives rise to clean, orderly work stations such as the cleaning trolley, lube station and change parts rack shown to the left.
It is also important to carry out a post mortem on the continuous improvement process - what worked, what didn't and what would the team members do differently next time.