Improve - Theory of Constraints
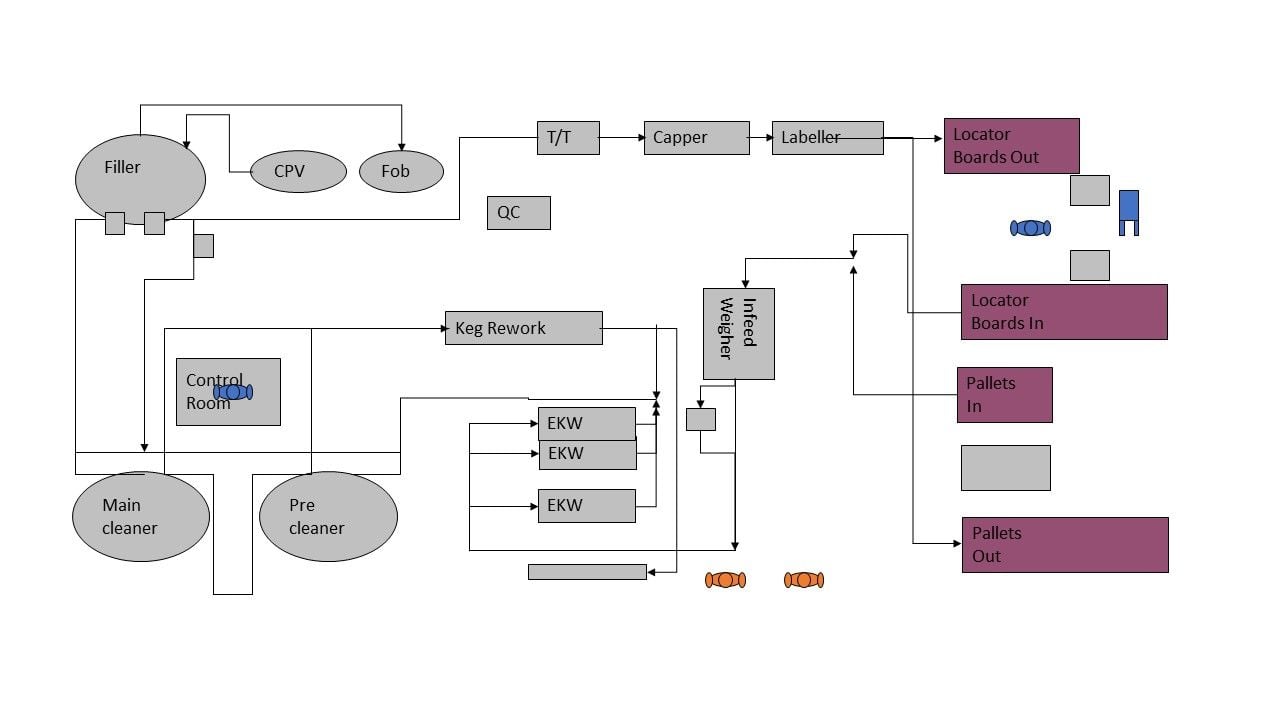
Zero Carbon Engineering were first involved in 1996 with "Theory of Constraints" when looking at both whole site operations and also at looking at improving the effectiveness of individual production lines. Its use is very effective in identifying how to remove waste and make optimise the performance of a process.
The theory of constraints (TOC) is an overall management philosophy introduced by Eliyahu M. Goldratt in his 1984 book titled "The Goal", that is geared to help organizations analyse and drive improvement.
The underlying premise of the theory of constraints is that any organisation or process can be measured and controlled by variations on three measures: throughput, operational expense, and inventory.
Inventory is all the money that the system has invested in purchasing things which it intends to sell. Operational expense is all the money the system spends in order to turn inventory into throughput. Throughput is the rate at which the system generates money through sales.
In the example above a beer keg filling line, the DMAIC issue defined was "can we get more output". Each stage of the process was clocked by stop-watch and any stoppages plus cause noted. The line was nominally specified as 1,000 beer kegs per hour, but the trials identified that with the balancing of machines speeds, the throughput speed could be increased by 8% without any impact on product quality.
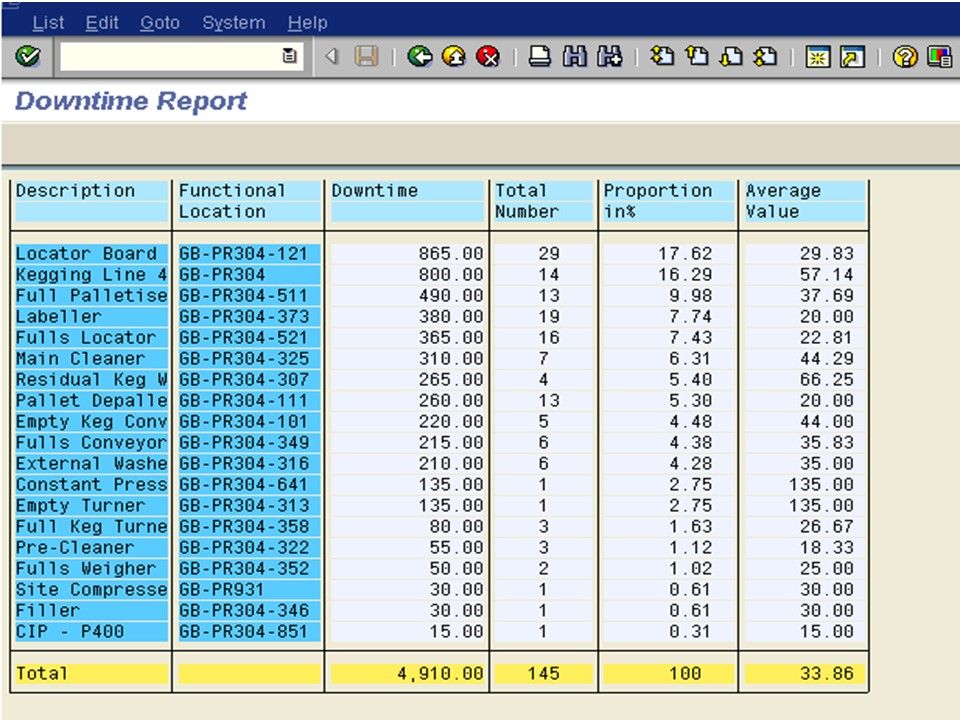
The largest cause of downtime was damaged plastic locator boards - and a process was put in place to filter out damaged boards before they got to the automated plant.
There was nowhere for the operators to base themselves, so to keep them comfortably near to the line, a glazed control station with SCADA, a phone, kettle/coffee was built at the centre of the line.
This improved reaction time to any incidents - reducing downtime.
The issues with the palletiser was caused by damaged pallets and again these were removed before they got to the automated plant.
The issue with the labeller was shown to be a timing problem and a standard operating procedure was produced so that the problem did not arise.
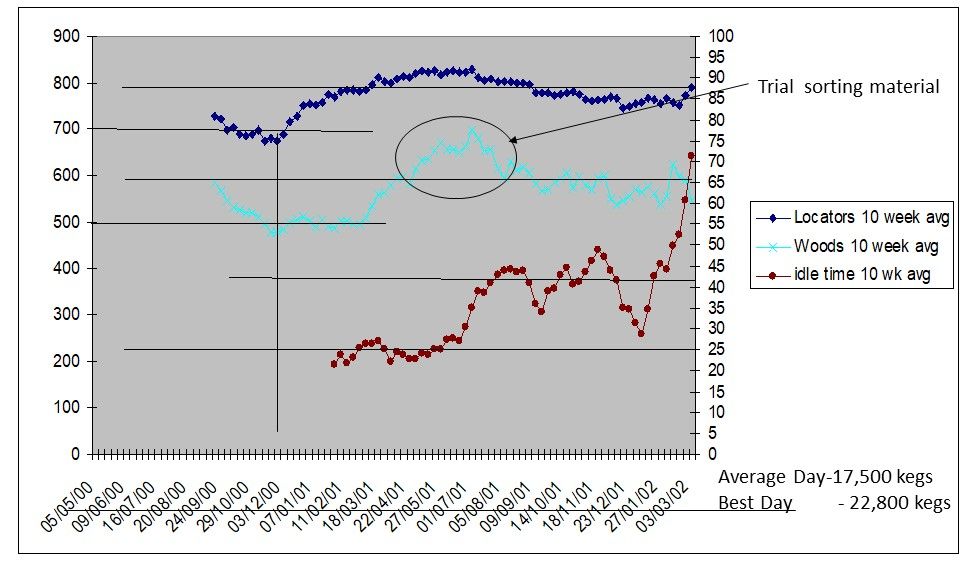
The table right shows the results over a ten month period. Performance on locator boards increased by 14% and was maintained. A trial to removed damaged returnable pallets increased productivity by 40% and got close to locator boards.
Unfortunately the supplier of returnable pallets was unable to maintain quality and the output dropped down to a lower but still improved level.
Idle time (the time when production was complete and the line was not used) increased significantly. This time was then used for training and further improvement activity.
The underlying principles behind this can be applied to any manufacturing process line and also to may other business processes.